Materials & Technologies
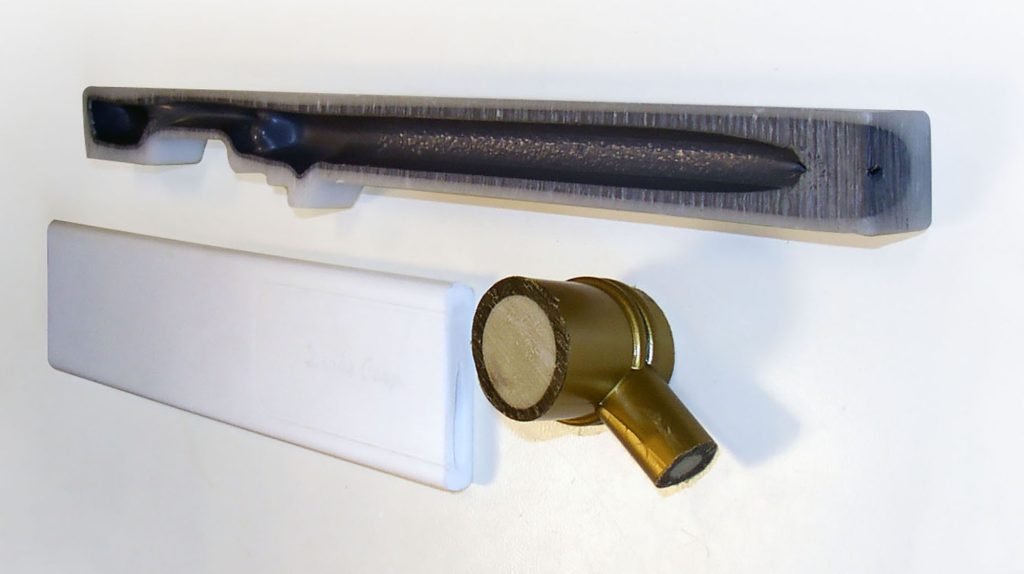
We use all major thermoplastic resins including PP, PS, ABS, SAN, PC. We do specialize in the following processes:
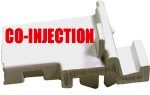
Co-injection molding is the technique of injecting two materials (usually the inner material is enriched with a chemical foaming agent) into a mold in a controlled sequence in order to produce a thick molding with a compact outer skin and an inner core of structural foam. Co-injection molding is the best way of manufacturing thermoplastic items with a section of 5 mm or more (0.2” or more), requiring a smooth impeccable surface. This particular process overcomes issues like warping, cracking, shrinkage and much of the built-in-stress found in conventionally molded thick components. Important savings can be achieved by using a quality material and coloring in the skin/outer layer while using recycled or lower grade materials in the core. Beyond the savings, brilliant technical solutions can be obtained by pairing compatible materials enhanced with different additives which leads to radically different properties in the skin and in the core while still working as one in a single component.
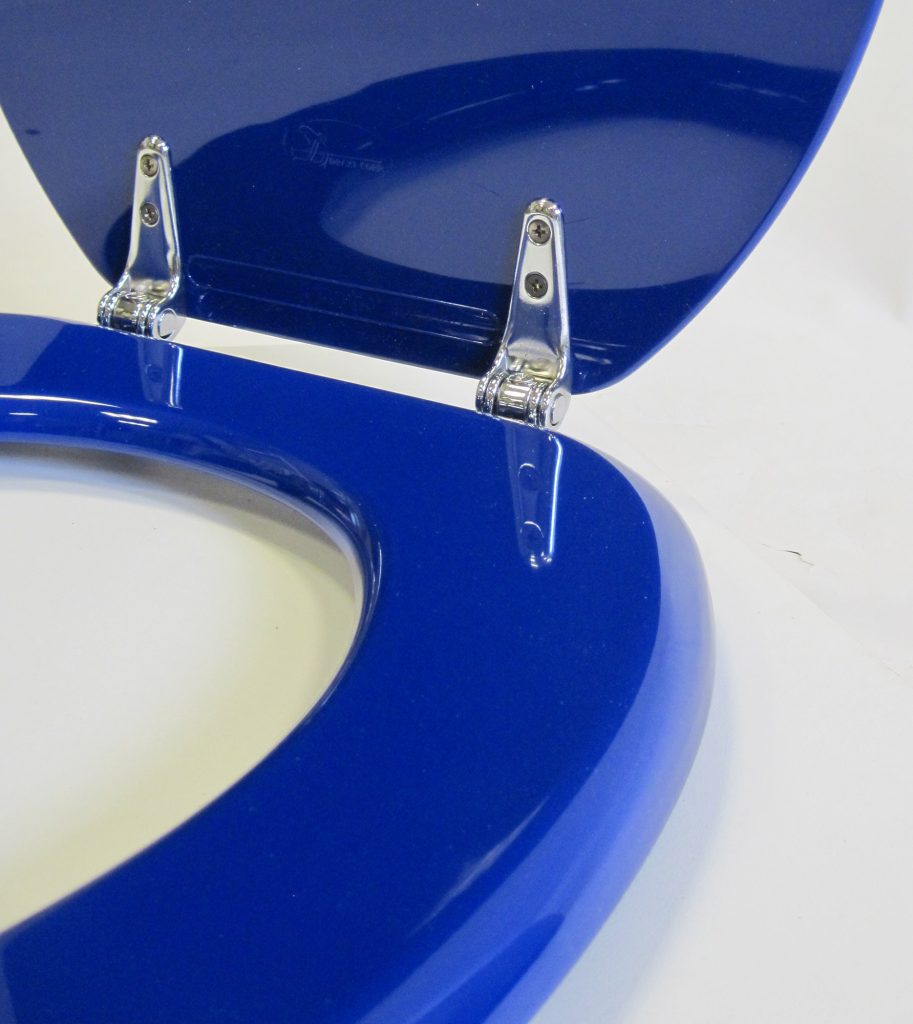
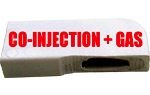
Co-injection molding with Gas assist is the technique of injecting two materials (usually the inner one enriched with a chemical foaming agent) into a mold and using high pressure gas to empty the core. This is one of the best ways of producing a very thick but lightweight component and the pairing of two different but compatible materials with different properties working as one. The foaming of the inner material is counterbalanced by the high pressure gas injected into the mold cavity creating a variable density wall that can be controlled by timing the gas injection (compact high density skin material on the outer visible wall, a lower density foamed 2nd material showing increasing higher density approaching the inner wall of the hollow core).
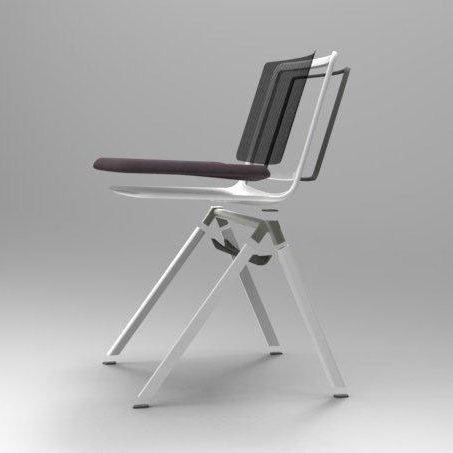
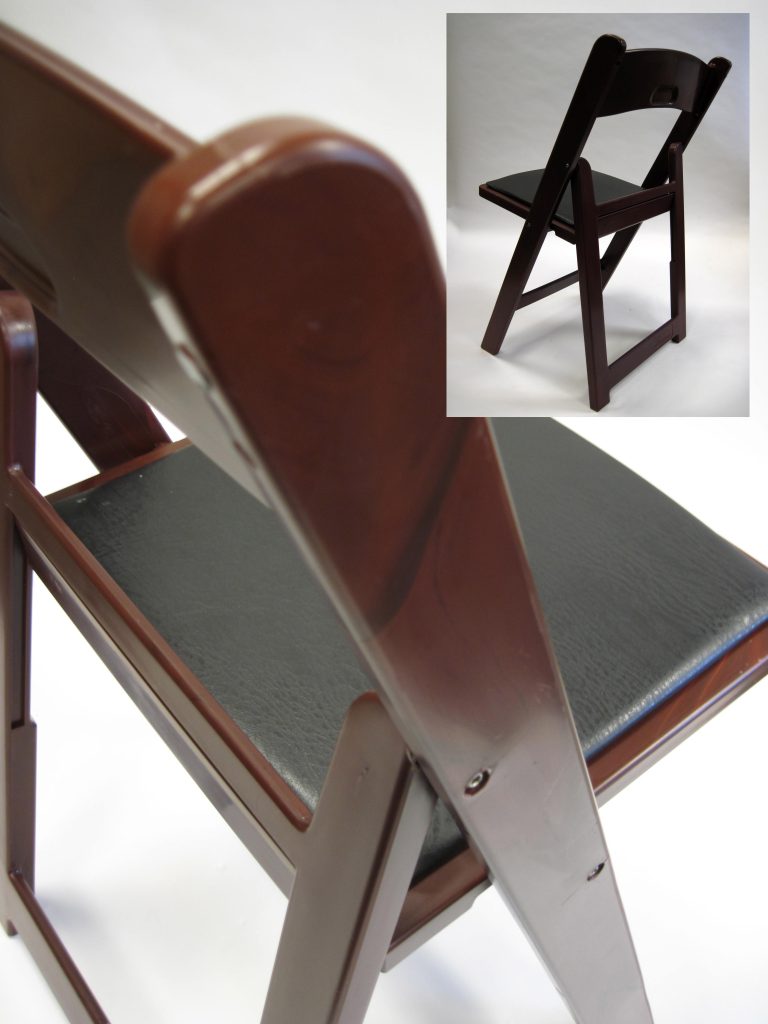
Structural Foam Molding is used to produce bulky items overcoming issues like warping, cracking, shrinkage and much of the built-in-stress found in conventionally molded thick components. The surface aesthetic associated with structural foam molding can be exploited to obtain a wood-like effect through additives, material coloring and tool engraving.
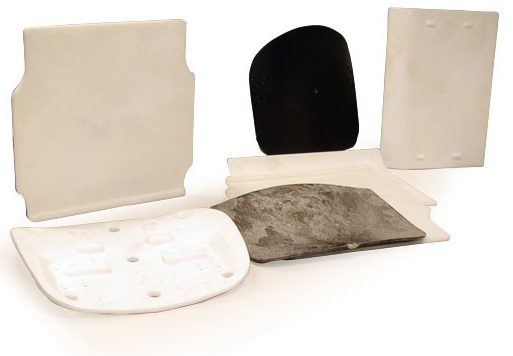
Our Capabilities
• Parts and components up to 10kg [22 lb]
• Platens up to 1100 mm [43”]
• Columns up to 850 mm [33 1/3”]
• Min. Mold Thickness 300 mm [11 2/3”]